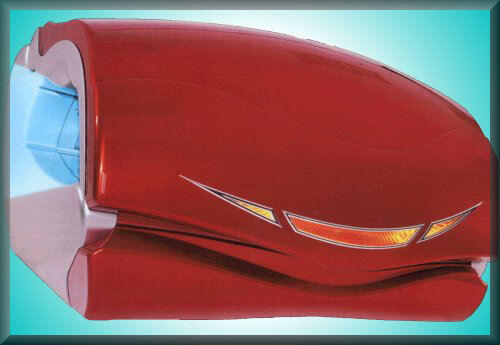
Arrowhead has extensive experience in fiberglass tanning bed fabrication, having manufactured custom fiberglass covers for a variety of high-end designer tanning bed models. These premium tanning beds demand not only precision-molded parts, but also detailed sub-assembly, finishing, and quality control to meet the high expectations of both manufacturers and end users.
Our work in this space involves more than just molding fiberglass components—we deliver complete, production-ready assemblies that reflect the luxury nature of the product. Each fiberglass tanning bed cover we produce undergoes meticulous surface prep, secondary painting, and careful inspection to ensure every part meets Class-A finish standards. These covers are often installed in upscale salons or spas, where aesthetics, durability, and flawless appearance are essential.
Arrowhead’s fiberglass tanning bed fabrication process includes tight adherence to customer specifications, high-level cosmetic finishing, and optional custom painting services. We understand the importance of form and function in the tanning bed industry, and we deliver components that match both design intent and technical requirements. Whether your project involves a new design or ongoing production, Arrowhead provides the craftsmanship and consistency to support your brand’s reputation for excellence.
Let us bring your next fiberglass tanning bed fabrication project to life with precision, attention to detail, and unmatched quality.
The open molded fiberglass hood is a popular solution for large, contoured components in the transportation industry—especially in applications like buses, trucks, and specialty vehicles. One of the key reasons fiberglass is the preferred material is the significantly lower tooling cost compared to other molding processes. This is especially important for large parts that feature compound curves, complex surfaces, or molded-in details. Open molding allows manufacturers to produce durable, cost-effective hoods without investing in expensive, multi-cavity tooling systems.
An additional benefit of using an open molded fiberglass hood is the material flexibility it offers. The type and quality of fiberglass reinforcement—such as chopped strand mat, woven roving, or multi-axial fabrics—can be selected based on the strength, weight, and cost requirements of the project. This customization enables design engineers to fine-tune performance characteristics, ensuring long-term durability with minimal added weight. This is particularly advantageous in industries where reducing vehicle weight can lead to increased fuel efficiency and improved overall performance.
The open molding process also provides flexibility in integrating functional features into the hood. Structural brackets, reinforcing ribs, hinge mounts, and other hardware can be mechanically fastened, laminated in place, or bonded to the backside of the part during or after the molding process. These additions enhance both the strength and usability of the hood, allowing for seamless assembly with surrounding vehicle components.
Arrowhead specializes in producing high-quality open molded fiberglass hoods and similar components, offering engineering support, in-house tooling, and precision manufacturing to meet your unique project requirements. Whether you need a single custom prototype or a low-to-medium production run, open molded fiberglass offers the versatility, cost savings, and performance you’re looking for.
Request a Custom Molded Fiberglass Fabricated Part Quote
Product Features
Material | Fiberglass Reinforced Plastic |
Process | Open Molded Fiberglass with Secondary Assembly and Finish Painting |
View Other | Molded Fiberglass Products |